Shaped springs, flat springs and leaf springs are among the oldest types of metal springs and have established themselves as indispensable construction elements in numerous branches of industry. Today, they are an integral part of a wide range of applications, particularly in mechanical engineering, vehicle construction, precision engineering and electrical engineering. Their central property – absorbing mechanical energy through deformation, storing it and releasing it again when required – is used in a variety of ways (is unique). This ability to store and convert mechanical energy makes them the ideal construction component for force and displacement compensation.
Relevant requirements for the development and manufacture of flat, shaped and leaf springs:
- Suitable materials which, in addition to high strength and formability, also have additional technical properties such as heat resistance, electrical conductivity, anti-magnetism, etc., depending on the application.
- Basics for the calculation of flat, shaped and leaf springs that meet the technical requirements
- Advanced manufacturing processes for precise and economical production.
- Reliable measuring methods and test equipment for determining spring characteristics to check the spring function during and after production, as well as during experimental testing in the application.
The development of assemblies in which form springs, flat springs and leaf springs are used is often associated with experimental effort. There are many reasons for this: on the one hand, springs are often only included in the design process at a late stage, on the other hand, the existing calculation methods do not always adequately capture the real operating conditions. In addition to extensive experience in the classic design of flat, shaped and leaf springs, the finite element method (FEM) is now increasingly being used as a calculation tool.
Table of Contents
Applications for shaped springs, flat springs and leaf springs
The applications for springs made of flat material are countless and unmanageable. They range from simple leaf springs to complicated flat springs and shaped springs that are precisely adapted to the geometry of the surrounding components. Despite this diversity, it is possible to classify them according to function, intended use and spring shape.
Classification of metal springs according to intended use:
- Storage elements > storage of mechanical energy (energy storage) through reshaping (drive springs and winding mechanisms)
- Measuring elements > use of the linear relationship between force and distance (spring balance, force and torque sensors)
- Vibration and damping elements > absorbing shocks and vibrations (compensating springs, suspension springs)
- Rest elements > provision of preload forces and restoring movements (locking elements and contact bridges)
- Bearing elements > force distribution tasks for movements within a limited range (vibration compensation)
Subdivision into straight, curved, coiled and disk-shaped springs:
Straight flat springs are often used for contact systems of electrical switching devices, for example in relays. The contact springs made of flat material can be installed preloaded in this way. The switching paths are reliably closed by the existing spring forces.
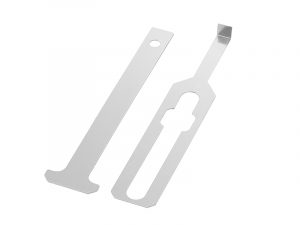
Curved flat springs one differentiates in curved leaf springs and shaped springs . In the case of the curved leaf spring, the spring is composed of straight and circular arcs. Any spring shape adapted to the task at hand is possible for shaped springs. The calculation is complex. Generally valid calculation models are not available. What is required is the many years of experience of the technician, who often determines the dimensions using known approximations and in experiments. The minimum bending radii in particular must be observed in the design guidelines.
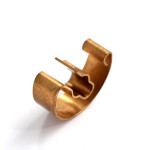
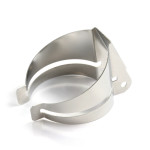
Under coiled leaf springs will Coil springs with and without space between coils and scroll springs combined. Disc-shaped flat springs , to which disc springs and Spring washers can be used as a single spring or in a combination of springs.
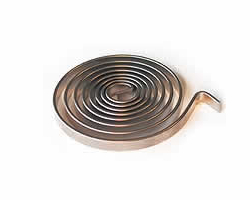
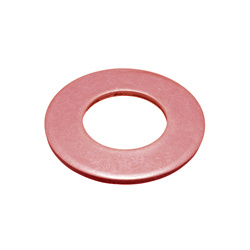
Design and construction
Numerous decisions have to be made when developing form springs, flat springs or leaf springs. These include the selection of the spring type, the specific spring shape, the choice of material, the determination of the dimensions as well as the consideration of the installation situation and the options for production and testing. The most important tools for these decisions are calculations of the deformation behavior of the springs. As there are usually more than two spring parameters to be determined, the basic design is carried out in an iterative process. A functional and strength verification must also be carried out for each designed spring. This involves checking whether the required spring rate, forces and travel are within the specified tolerances.
When determining the spring geometry, manufacturing and material-related aspects must be taken into account in addition to the functional requirements in order to make production as efficient and cost-effective as possible. The design of metal springs therefore requires special knowledge and experience in the areas of cold forming and heat treatment. After all, the geometry of the spring not only determines its reliability, but often also the functionality of the entire product in which it is used.
Manufacturing
Flat springs, shaped springs and leaf springs are manufactured according to requirements, shape and quantity using the pure bending / stamping and bending process or by laser cutting with subsequent forming by bending, stamping and edging. There are no limits to the shaping of flat or shaped springs. Final surface treatments such as vibratory grinding, barrel finishing, phosphating, burnishing, galvanizing, painting, etc. round off the production process. Furthermore, the springs can be installed directly in the assemblies provided. The selection of spring materials is extensive: in addition to normal spring steels, stainless steels, non-ferrous metals and collar metals are available in strip or plate form.
Material thickness: 0.1 to 3.0 mm
Band widths: 1.0 mm – 150 mm
Panel sizes: 1500 x 2500 mm
Production technology: lasers, embossing, punching, bending, grinding, assembling
Surface technology : Tumbling, phosphating, burnishing, galvanizing and painting … other surfaces on request
Well-founded and long experience is necessary for the optimal production of individual shaped, leaf and flat springs. Due to the individual and complex design, a standardized design and calculation is rarely possible. This is why Gutekunst Formfedern documents each production run in detail and uses this information for subsequent designs.
Gutekunst Formfedern works with you to develop a customized solution for your current task. Based on your drawing, CAD data, installation situation and functional description, we carefully check and calculate your requirements. If you are interested, simply use our inquiry form or send your documents directly to info@gutekunst-formfedern.de.
Federnanfrage
Benefit from the new Formfedern store
The new form spring store from Gutekunst Formfedern offers several advantages in the procurement of form springs, flat springs, laser parts and sheet metal parts. Thanks to its simple operation, transparent online price calculation and fast digital processing, it is a real support for designers, technicians and purchasers. At last, it is possible to configure, calculate prices, make inquiries and place orders for tailor-made formed metal parts in an uncomplicated and time-saving manner – around the clock and with maximum transparency.
Try it out for yourself at https://shop.formfedern.com
Formfedern-Shop
For more information: