The bending radius (r) is the radius measured after the bending process of a metal component or a shaped spring and flat shaped spring. However, the strength of the spring material decreases due to bending. The material thickness at the bending point is also reduced.
- α = bending angle
- β = opening angle
- L = material length
- r = bending radius
- s = spring steel plate thickness
Table of Contents
The bending process in detail:
During bending forming, the outer fiber or exterior (marked red in the figure) of the forming spring, flat forming spring or metal component is stretched. The inner fiber (blue, stands for inside), on the other hand, is compressed. Between the outer and the inner fiber lies the neutral fiber (green). This area is neither stretched nor compressed.
In order to exclude a reduction in quality due to compression and stretching, it is important to maintain minimum bending radii. This is the smallest possible bending radius of a material at which the workpiece does not break. If this value is undershot, cracks will appear on the outside and bruising on the inside. In addition, the cross-section in the bending zone can change. This means that there is a risk of the workpiece breaking.
Generally, therefore:
- larger bending radius = lower risk of breakage and reduction in strength
- smaller bending radius = greater risk of breakage due to thinner material thickness at bending point
How do you determine the minimum bending radius?
Each spring material has its own minimum bending radius. This depends on the composition of the alloy, the material thickness and the yield strength ratio. This is the ratio of the yield strength or elastic limit (Rp) to the tensile strength (Rm) of the material. For spring steel grades, this is usually over 85 percent. In comparison, the yield strength ratio of structural steel is only about 40 percent – lower values are also conceivable.
In order to determine the minimum bending radius, various factors must be taken into account. The following is an overview of the most important sizes:
- Spring steel type
- Spring steel thickness
- tensile strenght
- Bending method
- Bending tools
- Bending speed
- Rolling direction of the spring steel
- Pressing force
Elasticity is considered to be one of the main characteristics of spring steel. It is achieved in the manufacturing process by adding silicon (Si), manganese (Mn), chromium (Cr), vanadium (V), molybdenum (Mo) and nickel (Ni) to a special alloy. As a general rule, the elasticity of spring steels with higher tensile strength is lower than that of steels with lower tensile strength. For materials with higher tensile strength, the minimum bending radius must therefore be set larger.
For the different types of spring steel such as the normal Spring steel plate C75S, the corrosion-resistant Stainless steel grades 1.4310, 1.4568 and 1.4401, the non-magnetic spring bronze CuSn6 and the copper-beryllium spring steel CuB2 as well as the heat-resistant spring steels Nimonic 90, Inconel X-750 and 718, the exact minimum bending radii for Gutekunst Formfedern described and determined and managed in test bends.
What should be considered when bending?
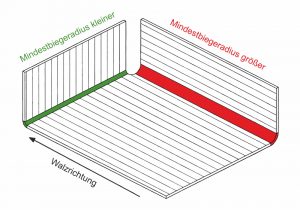
An important factor in bending forming is, among other things, the rolling direction of the spring steel sheet. This is because the stretching of the material during rolling creates a fibrous material structure. The elongation of the fibres always occurs in the rolling direction. If the steel sheet is bent along the rolling direction, it may break prematurely. The minimum bending radius must be larger in such a case. If, on the other hand, the workpiece – such as a shaped spring, flat shaped spring or metal component – is bent transversely to the rolling direction, a smaller minimum bending radius is possible.
In addition, the determination of the required pressing force also plays an important role in bending. In order to permanently reshape the spring steel, the value of the yield strength must be exceeded. If this is not the case, the metal returns to its original state. Only a load above the yield point causes plastic deformation. It is essential to ensure that the tensile strength of the spring material is not exceeded, otherwise the material could be damaged.
To ensure that the material does not tear or even form crimp folds, especially with thicker material and small bending radii, it is necessary to have a wide range of different tools available for the various bending radii.
Spring design of Gutekunst Formfedern
With Gutekunst Formfedern you do not have to worry about such possible problems. This is because Gutekunst develops the right flat form springs or form springs together with you right from the start.
If you are interested, simply send us your application for a flat shaped spring or shaped spring with the desired properties via our enquiry button shaped springs or to info@gutekunst-formfedern.de.
Anfrage Formfedern & Blattfedern
Further information can also be found here: